引 言
在我国城镇化率依然具有增长空间的背景下,城乡建设、基础设施建设等领域仍存在大量建设需求。建筑材料作为建设领域的上游行业,其碳排放情况会对下游领域的碳中和进程产生巨大影响。
水泥是建材行业中碳排放量最大的子行业,同时也是制造业领域仅次于钢铁的第二大碳排放行业,行业整体的节能减排对于我国总体实现碳中和愿景意义重大。2021年,中国建筑材料联合会发布《推进建筑材料行业碳达峰、碳中和行动倡议书》,明确提出建材行业要在2025年前全面实现碳达峰,水泥行业更是要在2023年前率先实现碳达峰。
中大咨询将从水泥行业碳减排的必要性入手,判断水泥行业碳排放的来源及其构成,并深入分析其在“双碳”目标下的发展趋势。
一、 水泥产量位居高水平,行业碳减排任务艰巨
我国是全球最大的水泥生产国家。21世纪以来,随着城镇化率的提升,水泥作为重要建材,需求愈发旺盛。我国水泥产量一路攀升,并于2014年达到24.92亿吨的最高峰(图 1)。此后,水泥产量进入平台期,2020年国内总产量约为23.95亿吨,占全球水泥产量的53.84%(图 2)。我国水泥熟料产量近几年也现出上升的趋势,截至2020年底达15.79亿吨。
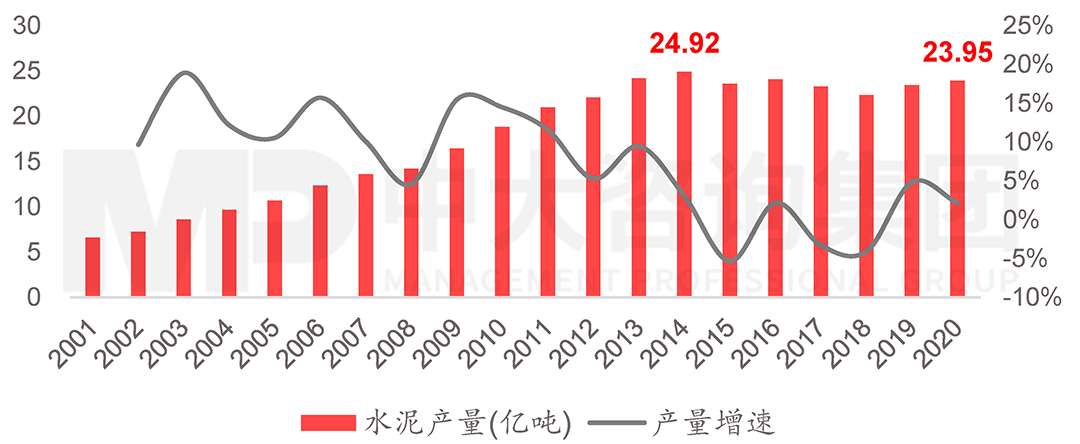
图 1 2001-2020年我国水泥产量及增速,数据来源:国家统计局;中大咨询分析
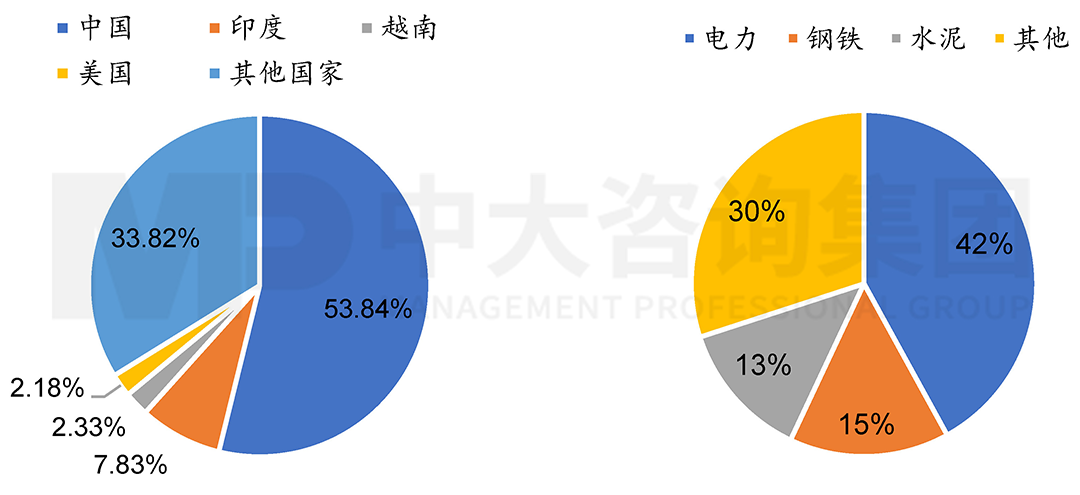
图 2 左:2020年全球水泥产量各国占比;右:2019年我国碳排放主要部门结构,数据来源:CEADs;公开资料整理;中大咨询整理
我国水泥产量长年来居高不下,行业整体碳排放也在逐年上升。水泥产量的上涨导致水泥行业碳排放量持续走高,2020年达到历史最高值13.84亿吨(图4)。2019年,水泥行业碳排放约占全国总量的13%(图3),是仅次于电力、钢铁行业的二氧化碳“排气筒”,控制水泥行业的碳排放成为了我国实现“双碳”目标的重点工作。
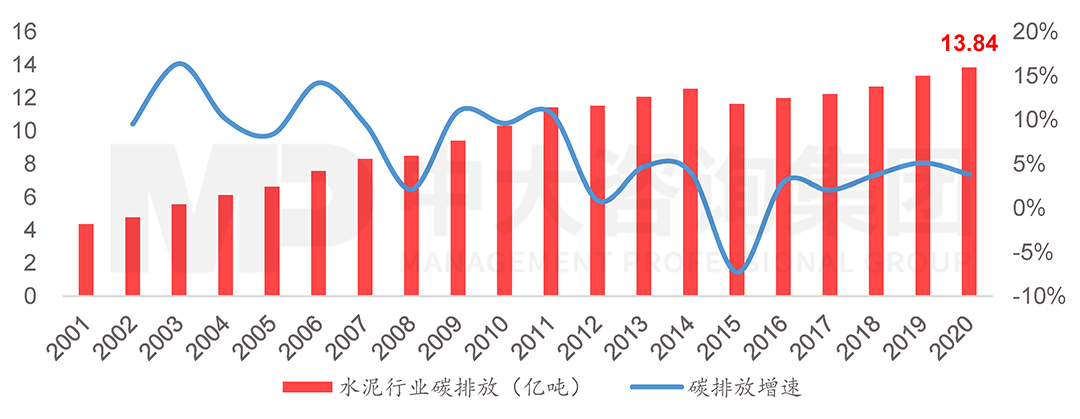
图 4 2001-2020年水泥行业碳排放量及增速(注:根据石灰石分解碳排放占比推算行业总排放),数据来源:Our World in Data;中大咨询分析
2015年巴黎协议的2摄氏度协议(2DS)约定,全球水泥业必须在2050年达到碳中和的目标,在2030年必须达成减碳40%。目前,我国水泥熟料碳排放系数(基于水泥熟料产量核算)约为0.86,即生产一吨水泥熟料将产生约860公斤二氧化碳,折算后我国水泥碳排放量约为597kg,与2DS协议要求(520-524kg)相比仍然偏高。因此,要完成巴黎协议2050年的终极目标,我国水泥行业的减碳工作迫在眉睫。
二、 水泥行业碳排放源头追溯
由于水泥生产的规模及其生产过程的特点,水泥工业是二氧化碳排放的主要来源之一,属于难减行业。
水泥的生产过程为“两磨一烧”,包括生料配料和研磨、窑内熟料煅烧和水泥熟料粉磨加工等环节,其中二氧化碳的直接排放包括原料煅烧的气体释放和熟料燃烧的能源消耗。(图 5)
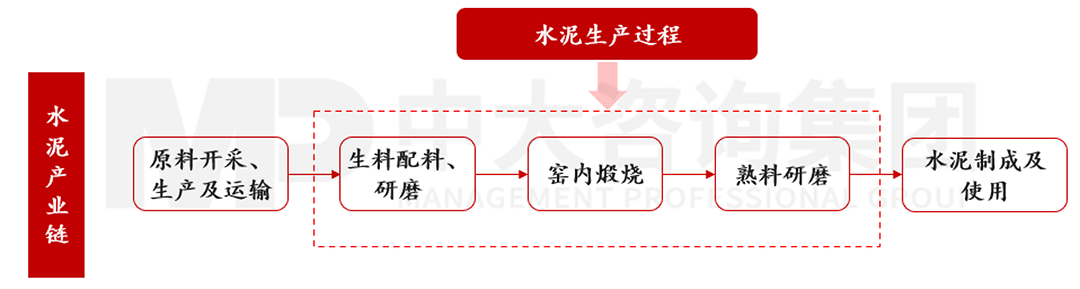
图 5 水泥生产全流程,资料来源:公开资料整理;中大咨询分析
水泥生产过程中的碳排放集中在熟料的生产程序中,主要来自石灰石的分解和化石燃料的燃烧,2020年分别占水泥碳排放总量的62%和29%左右。根据测算,来自燃料燃烧和熟料生产过程中的碳排放占比可以达到90%以上,其中60%以上来自石灰石分解(图 6)。由于石灰石作为原料难以替代,水泥行业减碳难度相对电力、钢铁行业大得多。
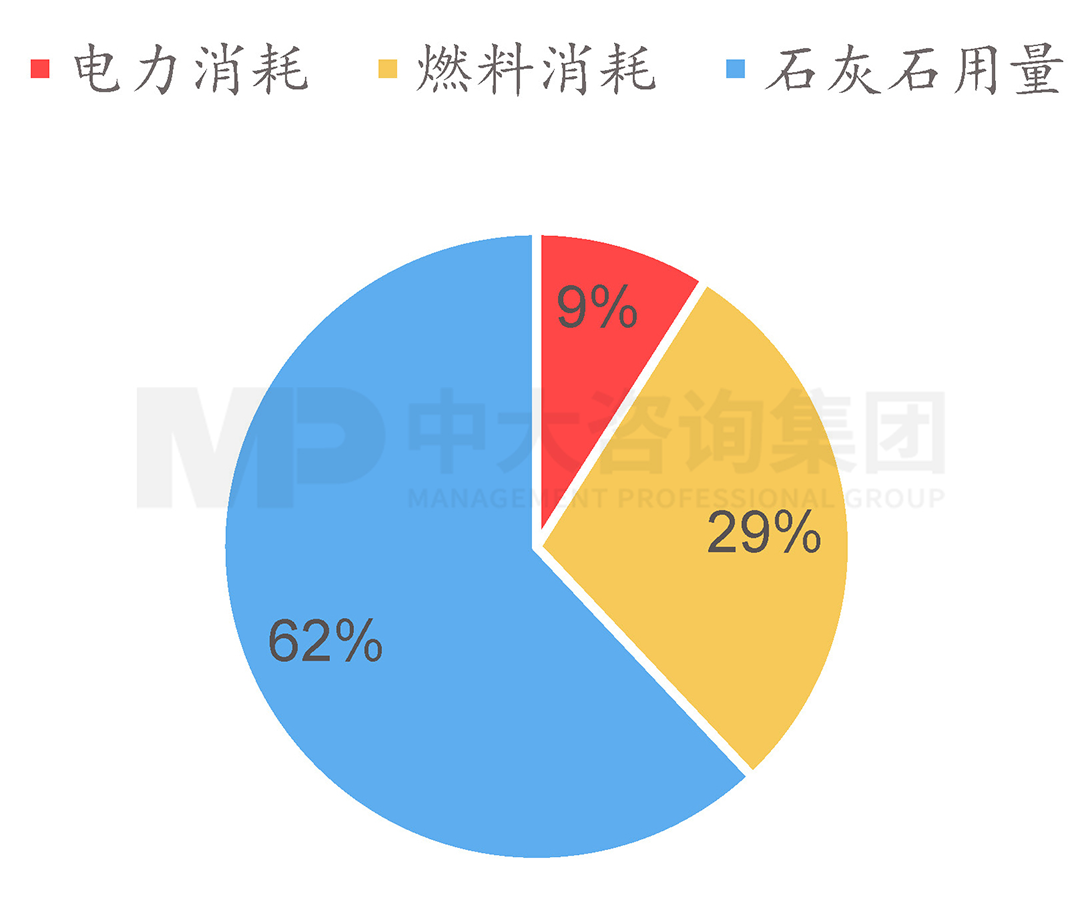
图 6 2020年我国水泥碳排放结构,数据来源:水泥大数据研究院;中大咨询分析
三、 “双碳”背景下,水泥行业如何寻求高质量低碳发展?
水泥行业的碳中和目前面临减排量大、时间紧迫等困难,需要在巩固去产能效果的前提下,运用减排技术减少水泥生产环节的碳排放。
01 行业层面:依靠市场与产业政策的结合,在控制产能的基础上逐步关注提升生产效率
控制产能产量并维持合理水平的产能利用率是目前水泥行业最直接有效的减碳方式。
“十一五”和“十二五”期间,由于部分企业急于追求经济效益、盲目扩张生产线,我国水泥行业存在严重的产能过剩。自2016年实施供给侧改革起,国家明确严禁水泥行业新增产能并开始淘汰落后产能,供需逐渐趋向平衡。截至2018年,我国新增水泥熟料产能有明显下滑,生产线新增数量也显著下降(图 7),限产限增的政策取得了良好效果。
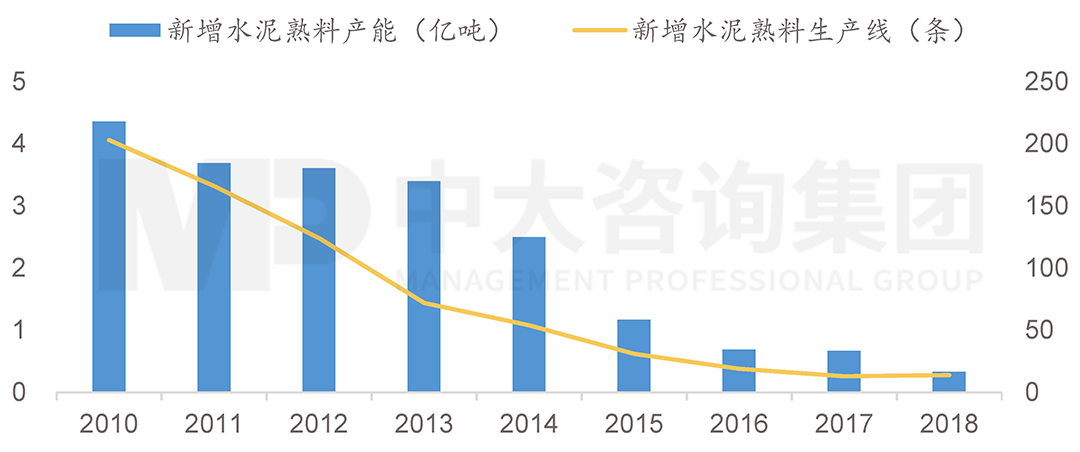
图 7 2010-2018年我国新增产能状况,数据来源:Wind,数字水泥;中大咨询分析
2021年12月发布的《“十四五”原材料工业发展规划》明确水泥产能只减不增,提出到2025年,产能利用率保持在合理水平,水泥产品单位熟料能耗水平降低3.7%,严格控制钢铁、建材等主要耗煤行业的燃料煤耗量。2021年,我国水泥熟料产能利用率能够基本维持在60%—80%之间(图 8)。未来的工作重点在于,保持较为合理的产能利用率,巩固供给侧改革去产能的成果,在保证下游需求得到满足的前提下进一步提高生产效率。
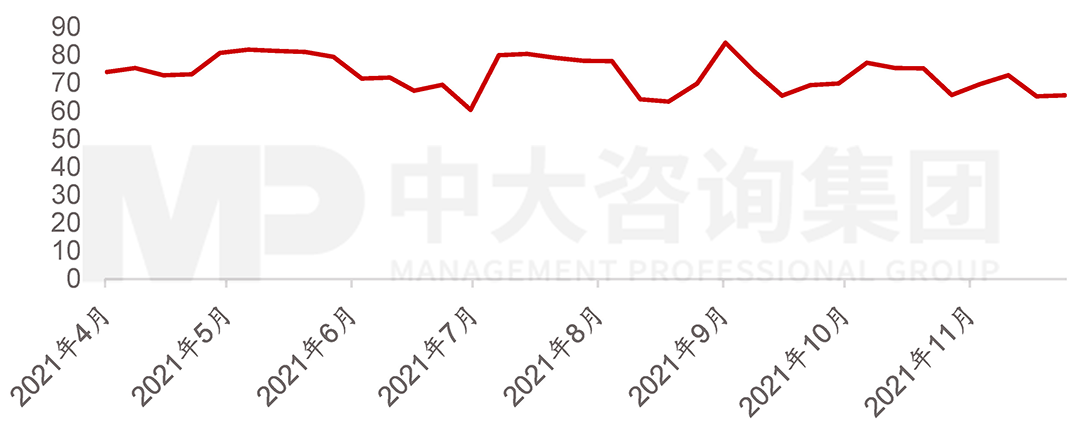
图 8 2021年4-11月我国水泥熟料产能利用率,数据来源:Wind;中大咨询分析
此外,水泥行业还需要通过推进兼并重组、产能减量置换、错峰生产等产业政策手段来控制产能(图 9),从而推进行业碳减排。
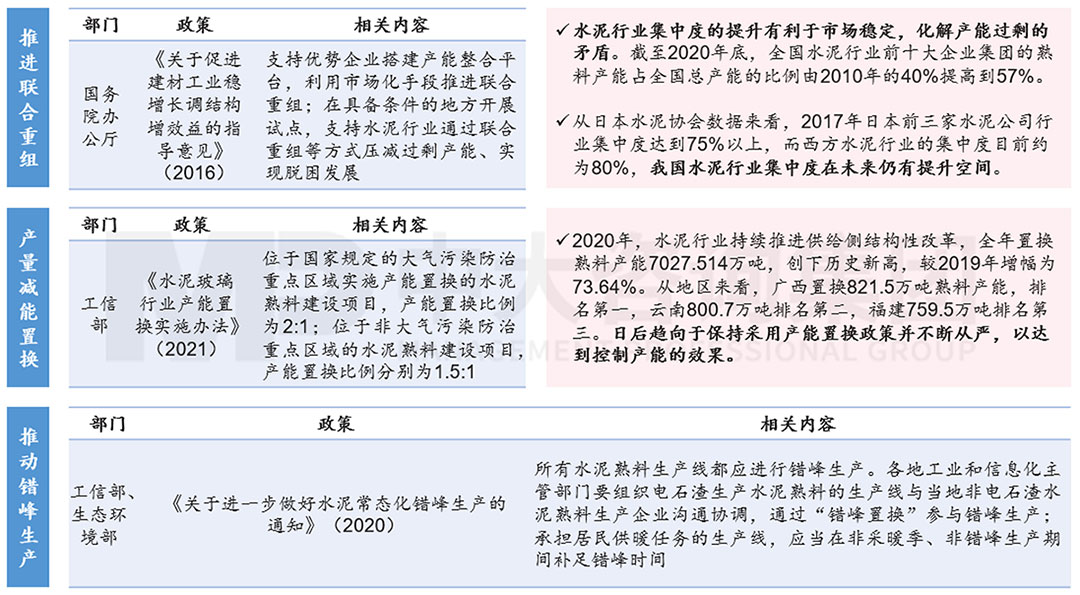
图 9 市场与产业政策结合控制水泥产能,资料来源:中国政府网,工信部,生态环境部,中国水泥协会信息研究中心;中大咨询分析
02 技术层面:合理运用相关技术降低水泥生产环节的碳排放
目前我国水泥企业全部采用了新型干法生产技术,整体处于国际先进水平,未来趋向于加强对减碳技术的研究和开发,如利用燃料替代、熟料替代、CCUS技术等方式促进水泥生产过程的减碳。但对于水泥来说,从长期来看很难有可以大范围、高比例替代石灰石的原材料,且考虑到成本因素,依靠相关技术来实现碳减排的空间可能较为有限。
(1)燃料替代:推进固体废弃物协同处置和生物质燃料替代,促进废旧资源循环利用
燃料替代方面,主要是执行“变废为宝”的重要理念,推进废弃物的协同处置,构建废弃物循环利用体系,减少水泥生产的碳排放,也有利于加强绿色低碳循环经济的发展。
▶ 水泥窑协同处置技术
水泥窑协同处置是水泥工业中一种新的废弃物处置手段,是将满足入窑要求的固体废物投入水泥窑,在进行水泥熟料生产的同时实现对固体废物无害化处置的过程。将废弃物作为煅烧环节的替代燃料,在降低生产能耗的同时减少了废弃物对环境的污染。(图 10)
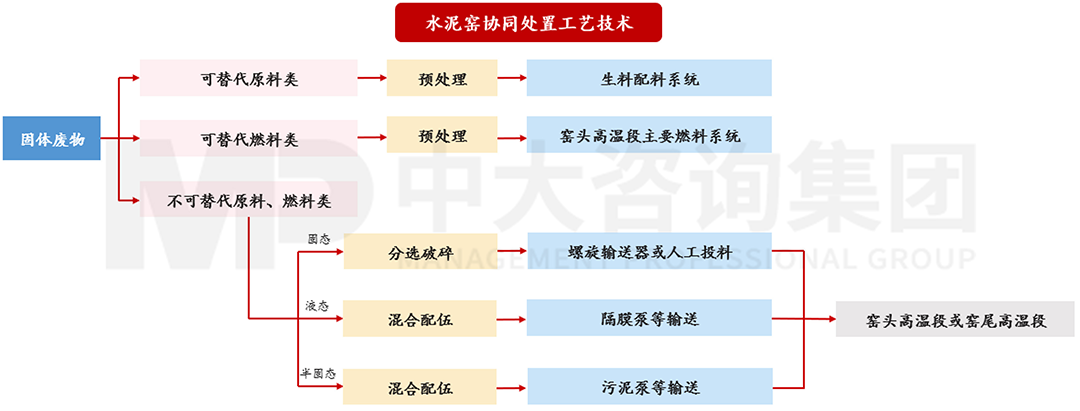
图 10 水泥窑协同处置技术原理,资料来源:水泥网,前瞻产业研究院;中大咨询整理
水泥窑协同处置技术在消纳固废、降低能耗等方面优势极大,未来将发展为成熟的碳减排技术。该项技术利用现有工业设施,不增加土地,环境扰动小,建设投资相对较少;且水泥窑具有高温煅烧和强碱性气氛,能够有效抑制二噁英等二次污染物的产生,促使水泥行业向绿色环保方向发展。截至2017年底,我国已建成水泥窑协同处置线约80条,全国利用水泥窑协同处置生活垃圾规模已达到每年500万吨,处置市政污泥能力近每年200万吨。今后水泥窑协同处置技术的覆盖率将大幅度提升,这种提升资源综合利用水平、替代原燃料的技术在行业内将愈发成熟。
▶ 生物质燃料替代技术
替代燃料的另一个来源是农作物秸秆、稻壳等生物质燃料,巧用生物质燃料替代技术能够起到显著的节能降碳效果。水泥行业中的生物质替代燃料包括棉花、高粱等农作物秸秆以及林木、生活垃圾等,均为可再生燃料,缓解了水泥工业对煤炭的依赖性。
生物质替代燃料技术不仅在水泥工业中能够帮助水泥熟料规模化生产,还能实现秸秆的无害化处置和循环利用,达到了节能减排的效果。以秸秆作为替代燃料为例,以5000t/d水泥熟料生产线按窑尾喷煤占70%计算,窑尾分解炉全部用秸秆代替燃煤,每年可减少碳排放37.3万吨(表 1)。由此看来,我国水泥行业在生物质替代燃料的推广应用上仍存在巨大空间。
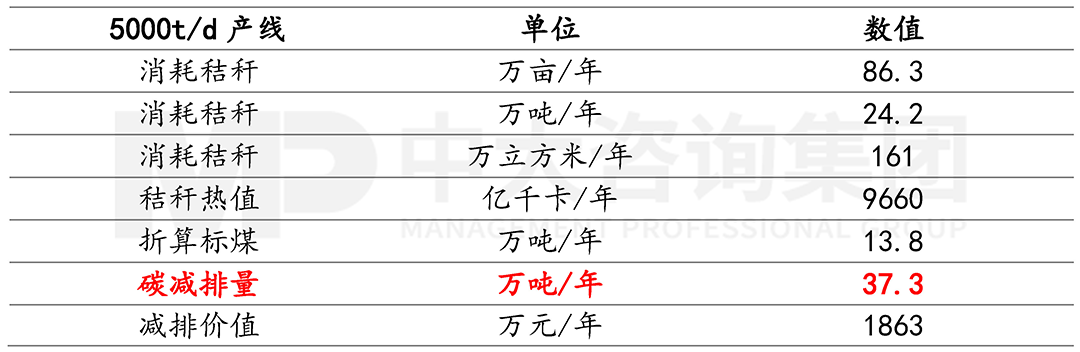
表 1 秸秆替代燃煤减排效果推算,资料来源:水泥网,根据公开资料整理;中大咨询分析
(2)原料替代:利用工业固废替代水泥原料,发展低碳水泥品种
水泥熟料替代技术有助于减少生产过程碳排放,包括以工业固废替代原料、应用新型低碳水泥和胶凝性材料、发展硫铝酸盐水泥等,但同时也存在一定限制。
▶ 将工业固体废弃物作为替代原料
水泥行业的主要原料为石灰石,而钢铁、火力发电等生产企业每年排放大量的钢渣、矿渣、电石渣、粉煤灰等工业固体废弃物,其有效化学成分与水泥熟料较为接近,具有作为水泥替代原料的可行性。我国每年产生约40亿吨此类固体废弃物,若将其作为水泥企业的替代原料,以年利用率20%计算,能够节省约8亿吨的天然矿产资源,具有极大的社会与经济价值。
▶ 大力发展硫铝酸盐水泥
硫铝酸盐水泥是我国自主发明的低碳水泥品种,可应用于各种工程建设,碳减排效果显著。由于不含高钙矿物C3S,生料中石灰石等钙质原料配入量比硅酸盐水泥约低30%,烧成温度比普通硅酸盐水泥低 100℃-150℃,熟料烧成过程中能够降低水泥碳排放约30%—40%(表 2)。

表 2 硫铝酸盐水泥与普通水泥碳排放量对比,资料来源:水泥网,公开资料整理;中大咨询分析
▶ 开发新型低碳水泥和应用低碳胶凝性材料
开发新型低碳水泥生产技术。国际上出现的煅烧粘土复合石灰石替代熟料的新型低碳水泥,主要是为应对未来可能出现的粉煤灰、矿渣类混合材短缺问题,该新型低碳水泥的28d抗压强度与参比纯硅酸盐水泥相当,而混凝土耐久性更优。
应用低碳胶凝性材料。水泥制品中应用胶凝性或有潜在胶凝性的混合材也可实现低碳排放,通过减少水泥中熟料占比,可显著降低水泥生产过程中与熟料生产产生的碳排放。
然而,替代原料发展存在一定的局限性。替代原料可能影响水泥质量,部分工业固废中含有一定比例的金属成分或氯离子等对生产过程和水泥性能有害的成分,掺入比例有严格的限制,需要进行预处理从而提高替代比例;替代原料的配套政策标准不够完善,市场接受程度不确定,且国家标准与替代原料所生产水泥的性质可能不匹配,目前较为缺乏配套的政策来进一步推动替代原料市场的发展。
(3)CCUS技术:水泥行业减碳的关键技术
作为水泥熟料生产环节碳减排的“兜底”手段,未来CCUS技术将充当极具重要性的技术路径,为水泥行业碳中和做出巨大贡献。国家发改委发布的《关于推动碳捕集、利用和封存试验示范的通知》提出要推动碳捕集、利用和封存(CCUS)试验示范,首次明确在火电、煤化工、水泥和钢铁行业中开展碳捕集试验项目。据测算,至2050年,水泥行业的碳减排潜力约50%依赖碳捕集利用技术,CCUS是水泥行业实现净零排放的可行性技术方案。
CCUS技术在水泥生产中的典型应用包括富氧助力水泥熟料煅烧和水泥窑烟气中二氧化碳的捕集利用等。其中,富氧燃烧采用高于普通空气的助燃气体,有利于入窑炉煤粉的充分燃烧;其投资、运行成本是相对而言最经济的,但仍面临一次性投资高、碳捕集利用成本居高不下的问题。
作为解决碳排放的有利技术,CCUS一直被广泛研究,我国已投运或建设中的CCUS示范项目约40个,捕集能力为300万t/a。然而,由于碳捕集技术对二氧化碳浓度有较高要求,水泥生产过程中二氧化碳的浓度不超过30%,需要提纯至95%以上方可进行捕集,因此CCUS技术在水泥行业的运用存在成本较高的问题。
CCUS是一种新兴技术,目前在石油、化工、电力等行业的应用也是以小规模的捕集示范为主。对于水泥行业来说,在考虑成本因素的情况下大规模工业化的应用是今后长期的发展趋势,依靠技术进步提高捕集效率、提升经济效益。
四、结语
水泥工业是我国建材行业中的支柱产业,也是制造业中的碳排放大户,是实现“双碳”目标的重要领域。水泥行业未来的低碳发展,仍然离不开控制产能产量的政策手段;从长期来看,在解决成本问题的前提下运用熟料替代、原料替代、CCUS等减碳技术也是实现碳中和愿景的重要途径。
参考文献
[1] 付立娟,杨勇,卢静华.水泥工业碳达峰与碳中和前景分析[J].中国建材科技,2021, 30(4):5.
[2] 方正建材专题报告:碳中和——推动水泥行业高质量发展,方正证券
[3] 李伟峰,马素花,沈晓冬.我国水泥工业减碳技术现实路径刍议[J].新世纪水泥导报, 2021,27(6):7.
[4] 《水泥行业低碳转型技术路线图》,IEA
[5] 吕宝玉,张海涛,赵绪礼.水泥行业碳达峰,碳中和之浅析[J].中国水泥,2021(9):4.